CANbus Plays Critical Role in Electric Vehicles
April 19, 2021
Controller Area Network
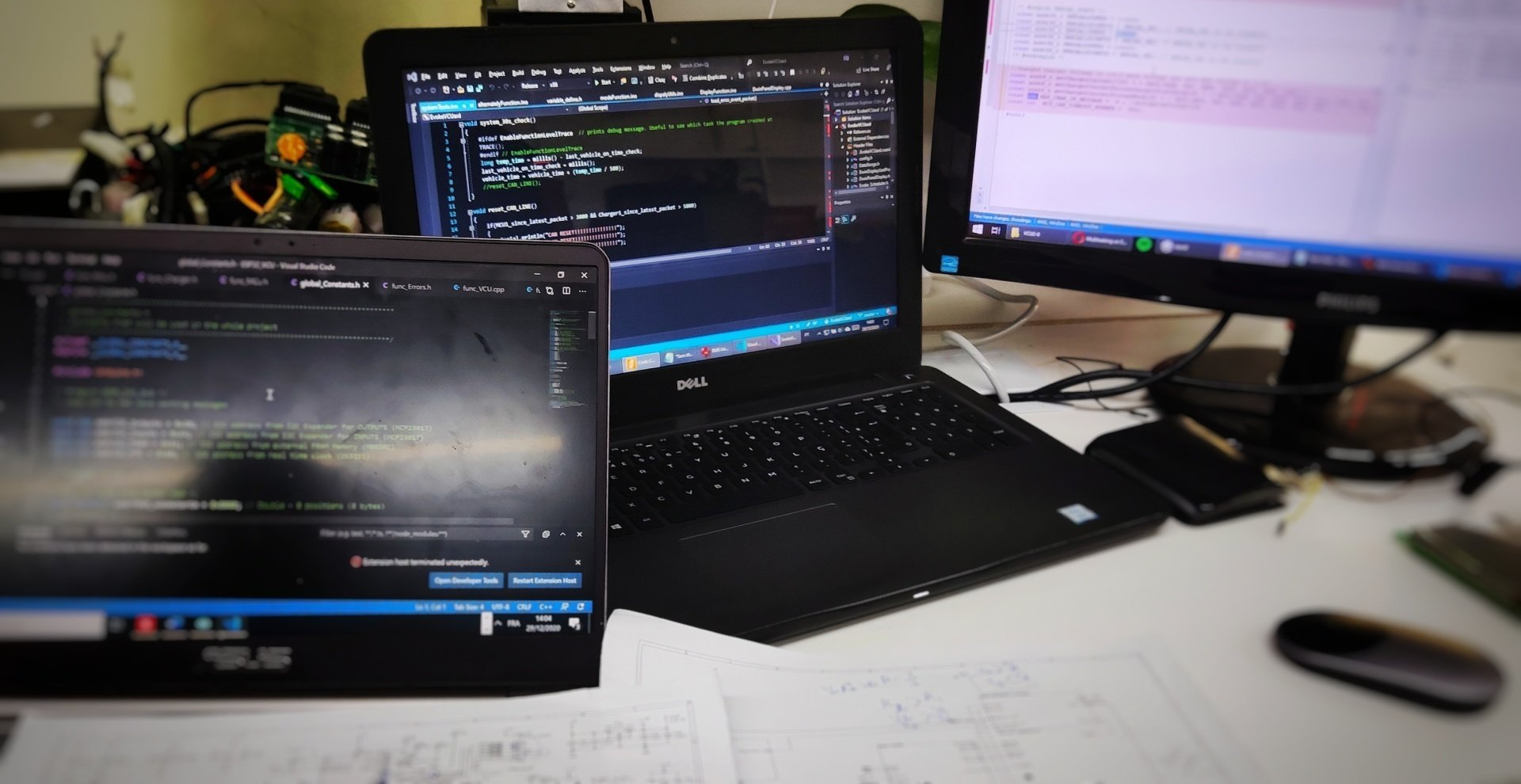
Communication between components and systems is common in today’s heavy-duty vehicles and equipment with CANbus (Controller Area Network). As technology continues to evolve, so have CANbus systems and the components which are connected to them.
Because of its communication capabilities, CANbus plays a critical role in electric vehicles. With the latter, it is especially important for components and systems to communicate with one another to ensure safe and efficient operation.
How is CANbus being utilized with battery powered systems and battery chargers?
The battery and the charger are very dependent on each other. Typically, the battery is the first largest expense in electric vehicles. So when we look for a battery solution, we want to make sure you are getting the most return on investment when you purchase our vehicle. What that means is getting the best performance out of it, the most life out of it, and the most cost-effective solution.New Paragraph
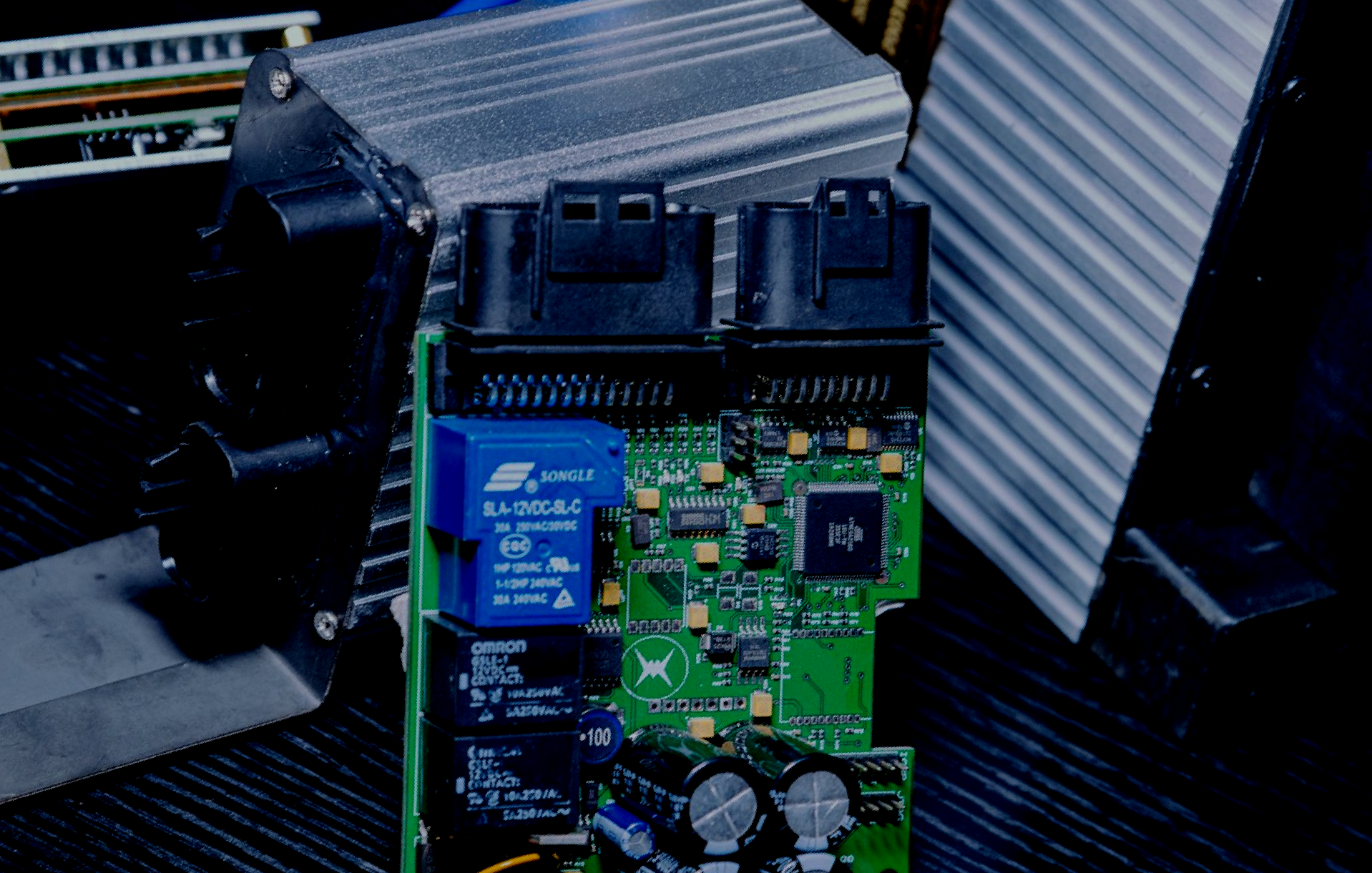
If you think back to lead-acid batteries, because there were no electronics involved you really had to characterize the battery and be as efficient as possible on that characterization. Whereas now that you have the flexibility to scale how you want to use that battery and the performance of the battery due to the communication path which most often is CAN communication, you are able to scale how and when the battery is doing what it’s doing.
As an example, with a lead acid battery, if you are scaling down on capacity, you could tell the capacity is going down in voltage, but you can't control how much power that battery is able to give out. With a lithium-ion battery and charging, you could tell the system you want to cap it at a certain point, and it will abide by that.
This is essential and important to the total cost of the battery because you could either enhance performance, or you could manipulate the battery through the communications to optimize the life at the expense of some performance. It gives you flexibility.
As an example, with a lead acid battery, if you are scaling down on capacity, you could tell the capacity is going down in voltage, but you can't control how much power that battery is able to give out. With a lithium-ion battery and charging, you could tell the system you want to cap it at a certain point, and it will abide by that.
This is essential and important to the total cost of the battery because you could either enhance performance, or you could manipulate the battery through the communications to optimize the life at the expense of some performance. It gives you flexibility.
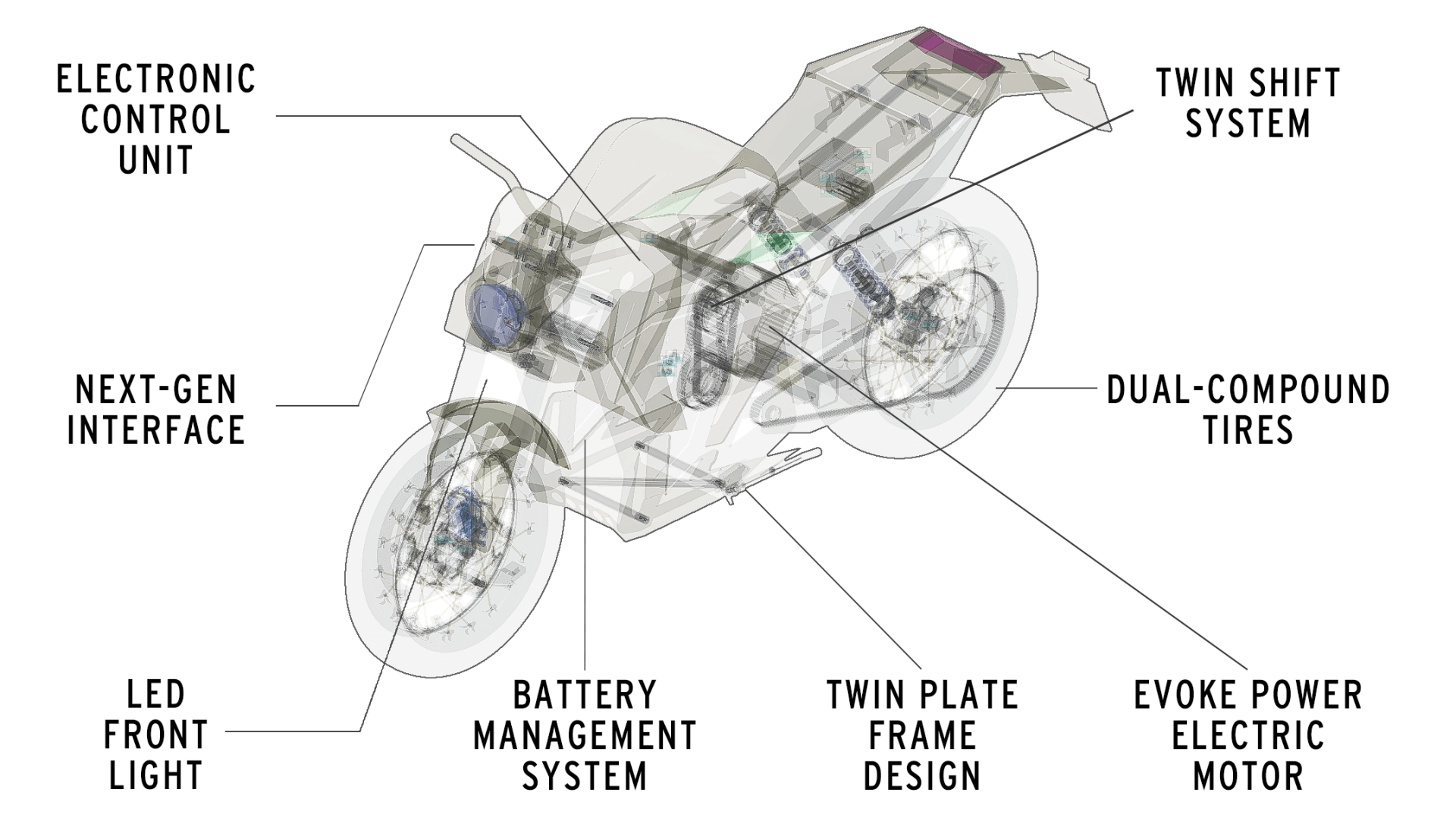
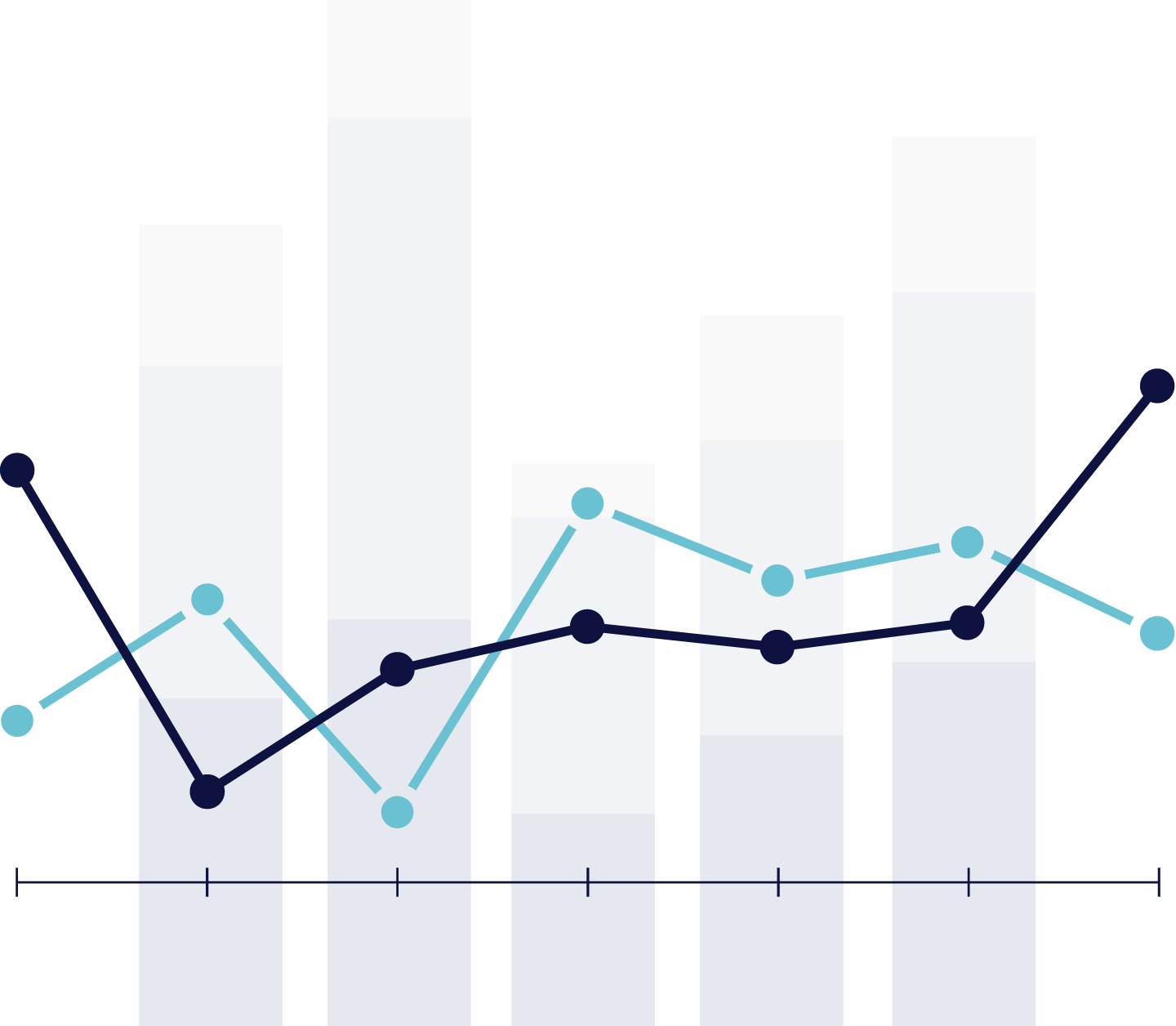
Data logging for electric vehicles offers numerous benefits. Firstly, it enables vehicle owners and enthusiasts to comprehensively analyse and evaluate their vehicle's performance. By recording essential parameters such as engine RPM, speed, throttle position, and braking force, among others, data logging facilitates the identification of areas for improvement, fine-tuning of vehicle settings, and tracking of performance changes over time. Furthermore, data logging serves as a valuable diagnostic and troubleshooting tool, providing crucial information about sensor readings, error codes, and system behaviour during specific events or conditions. This empowers mechanics and vehicle owners to identify problems accurately and make informed decisions regarding repairs or maintenance. For performance enthusiasts, data logging allows customization and optimization of vehicle settings, as continuous monitoring and logging of performance data enable precise fine-tuning of engine parameters, suspension settings, and other components. This approach helps achieve desired performance characteristics while maximizing efficiency. Importantly, data logging contributes to safety by providing insights into driver behaviour and vehicle performance, recording data related to acceleration, braking, speed, and other parameters. This information can be utilized for training purposes, monitoring driving habits, and assessing vehicle performance during critical situations. Thus, data logging proves to be an invaluable tool, offering multifaceted advantages for vehicle owners, enthusiasts, mechanics, and the automotive industry as a whole. When it comes to Evoke Motorcycles, collected data is used for identifying errors and potential areas of improvement in prototypes and other models. If an error or an abnormality comes up in the data, it can be easily noticed and traced to its origin, helping identify the root of the problem. Furthermore, using data brings valuable insights into driver behaviour and its variety. If one behaviour is more prevalent than the other, or there are many, the design or parameters can be manipulated to better suit the driver and make the driving experience much more pleasant and comfortable. In the future, data analytics are planned to be shifted in the hands of AI/ML providing instantaneous criteria and analysis on the go, as the data is being collected. This will fully automate the process and result in much more detailed diagnostics once the AI is sufficiently trained on the past data processes. All of the data is collected and stored within the vehicle, as this surpasses the limitation of servers. If the data is stored within a server in one country, a user in the other might not be able to access it. If the data is stored inside the Evoke motorcycle itself, the user can access it at any point and maintains full control of their own riding data. If there are any issues with the electric motorcycle, or the user would like to understand their riding data better, it can be easily sent to Evoke for review, bypassing any geopolitical limitations that would be otherwise present with the use of servers. The vehicle records up to 10 hours of riding data and is collected every 0.5 seconds. As of 2024, the 120 collected data points make up the five main data pools:
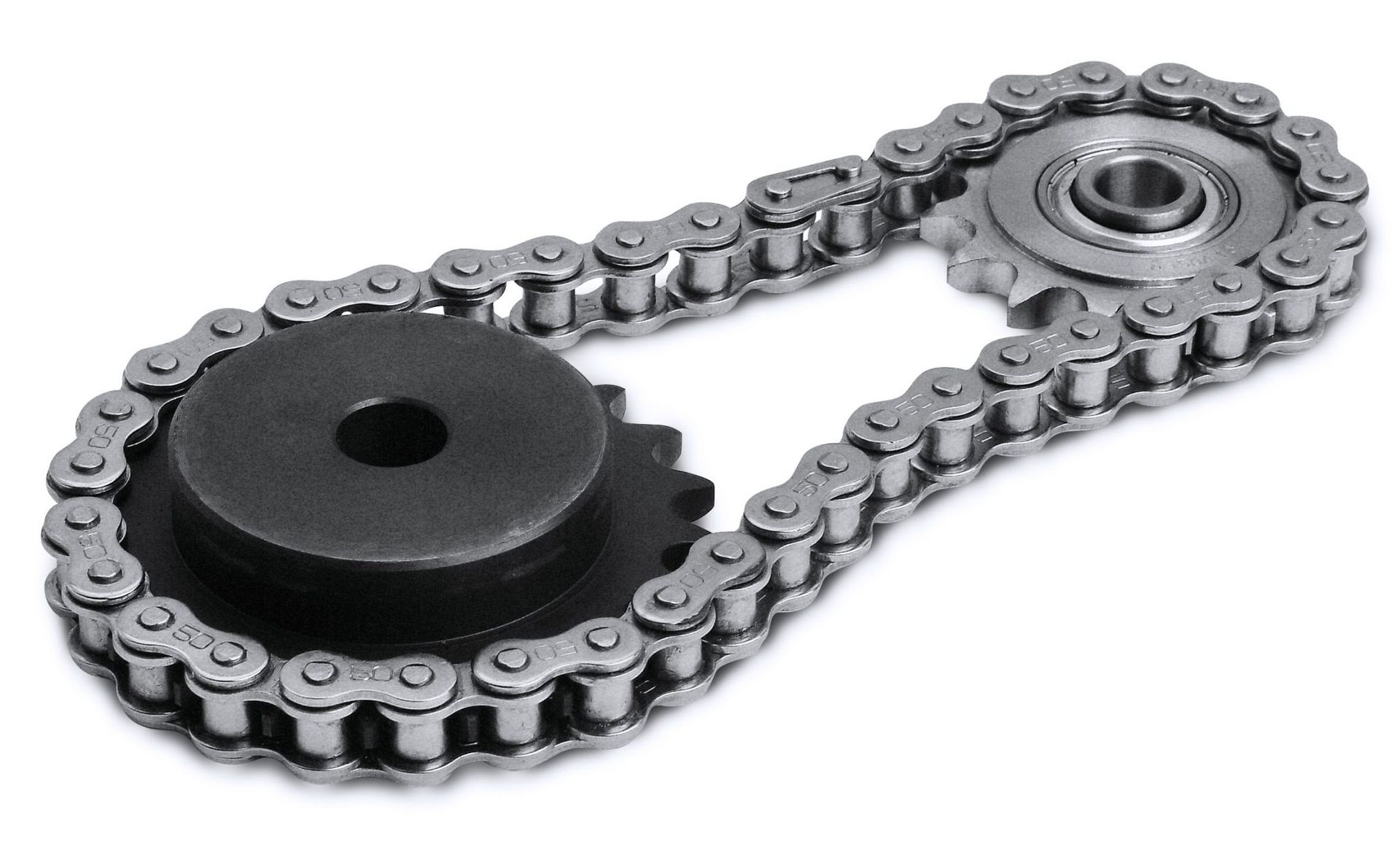
Vehicles, that run with combustion engines or ICEs rely on a jackshaft to efficiently distribute the produced power or simply optimise the conversion of energy to the wheels of the vehicle. ICEs cannot automatically regulate the speed of their rotation. In order to control it, different gears are introduced, to be able to increase and decrease the torque. If the jackshaft is part of a transmission system, it may have multiple gears or pulleys of different sizes attached to it. These gears or pulleys can have different ratios, allowing for torque conversion or speed adjustment. Gear ratio can be calculated via the formula below:
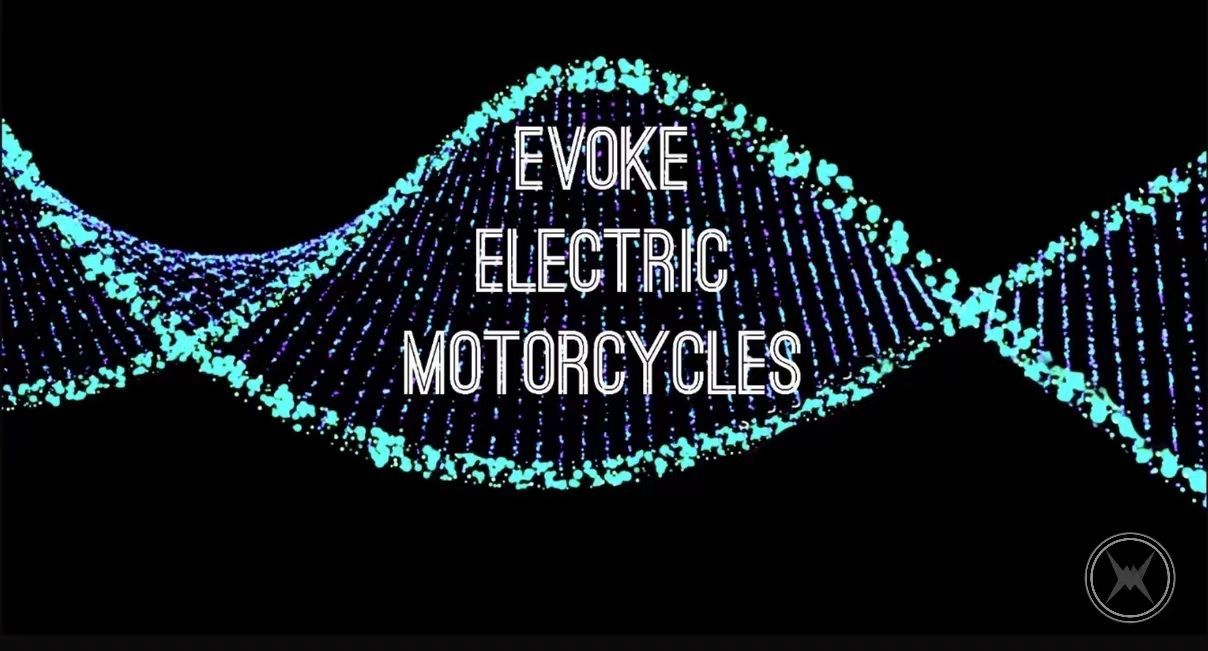
In terms of automotive there may be a handful of principles that determine the overall form and componentry present on a vehicle. Inescapable is physics, aspirational is performance but as another 20th century icon dictated, there's no escaping the bottom line and in manufacturing that means a need to establish and maintain a lean operational footprint.